Numerical analysis of discs based on carbon-nanofiber/Al2O3ZrO2 nanocomposite materials
Abstract
In this study, the behavior of three different discs consisting of AS4 carbon fiber, T-300 carbon, and Al2O3ZrO2 (nanocomposite) materials at constant temperature was investigated by the numerical analysis method. Nanocomposites are formed by the dispersion of nanometer-sized particles in a matrix. With the advantages that nanocomposites bring to the material, they increase heat resistance in general. Carbon fibers, on the other hand, are preferred in the aerospace industry and aircraft industry due to their high strength properties. In this study, it was assumed that the modulus of elasticity does not change with temperature. The temperatures applied to the discs are 45 ℃, 60 ℃, 75 ℃, 90 ℃, and 105 ℃, respectively. It has been observed that the radial and tangential stress values obtained at high temperatures are higher than at low temperatures. The Al2O3ZrO2 nanocomposite materials have found that the stresses occurring in the Al2O3ZrO2 (nanocomposite) disc are higher than the stresses occurring in the AS4 carbon fiber disc. The stresses obtained on the AS4 carbon fiber disc are T-300 carbon discs.
Keywords
Full Text:
PDFReferences
1. Ali A, Bayat M, Sahari BB, et al. The effect of ceramic in combinations of two sigmoid functionally graded rotating discs with variable thickness. Scientific Research and Essays 2012; 7(25): 2174–2188. doi: 10.5897/SRE11.619
2. Bayat M, Saleem M, Sahari BB, et al. Analysis of functionally graded rotating discs with variable thickness. Mechanic Research Communications 2008; 35(5): 283–309. doi: 10.1016/j.mechrescom.2008.02.007
3. Eldeeb AM, Shabana YM, El-Sayed TA, Elsawaf A. A nontraditional method for reducing thermoelastic stresses of variable thickness rotating discs. Scientific Reports 2023; 13(1): 13578. doi: 10.1038/s41598-023-39878-w
4. Belhocine A, Bouchetara M. Simulation of fully coupled thermomechanical analysis of disc brake rotor. Wseas Transactions on Applied and Theoretical Mechanics 2012; 3(7): 169–181.
5. Ramakrishna S. Mayer J. Wintermantel E, Leong KW. Biomedical applications of polymer-composite materials: A review. Composites Science and Technology 2001; 61(9): 1189–1224. doi: 10.1016/S0266-3538(00)00241-4
6. Mouritz AP, Gellert E, Burchill P, Challis K. Review of advanced composite structures for naval ships and submarines. Composite Structures 2001; 53(1): 21–42. doi: 10.1016/S0263-8223(00)00175-6
7. Gu GX, Takaffoli M, Buehler MJ. Hierarchically enhanced impact resistance of bioinspired composites. Advanced Materials 2017; 29(28): 1700060. doi: 10.1002/adma.201700060
8. Minatto FD, Milak P, De Noni A, et al. Multilayered ceramic composites—A review. Advances in Applied Ceramics 2015; 114(3): 127–138. doi: 10.1179/1743676114Y.0000000215
9. Hu T, Zhang Y, Hu L. Mechanical and wear characteristic of Y-TZP/Al2O3 nanocomposites. Industrial Lubrication and Tribology 2014; 66(2): 209–214. doi: 10.1108/ILT-08-2011-0059
10. Fang Y, Zhang Y, Song J, et al. Design and fabrication of laminated-graded zirconia self-lubricating composites. Materials & Design 2013; 49: 421–425. doi: 10.1016/j.matdes.2013.01.040
11. Ghabussi A, Mortazavi M, Betha R. Seismic performance of a cold-formed and hot-rolled steel wall system equipped with curved steel dampers. Structures 2023; 53: 296–316. doi: 10.1016/j.istruc.2023.04.053
12. Ghabussi A, Marnani JA, Rohanimanesh MS. Seismic performance assessment of a novel ductile steel braced frame equipped with steel curved damper. Structures 2021; 31: 87–97. doi: 10.1016/j.istruc.2021.01.073
13. Nayak P, Saha K. Elastic limit angular speed of solid and annular discs under thermomechanical loading. International Journal of Engineering, Science and Technology 2016; 8(2): 30–45. doi: 10.4314/ijest.v8i2.3
14. Lin FW. Elastic analysis for rotating functionally graded annular disc with exponentially-varying profile and properties. Mathematical Problems in Engineering 2020; 2020: 2165804. doi: 10.1155/2020/2165804
15. Yildirim V. Thermomechanical characteristics of a functionally graded mounted uniform disc with/without rigid casing. Journal of Aerospace Technology and Management 2019; 11: e2919. doi: 10.5028/jatm.v11.1008
16. Peng D, Chen S, Darabi R, et al. Prediction of the bending and out-of-plane loading effects on formability response of the steel sheets. Archives of Civil and Mechanical Engineering 2021; 21(2): 74. doi: 10.1007/s43452-021-00227-1
17. Lookpolymers. Hexcel® HexTow™ AS4 carbon fiber. Available online: http://www.lookpolymers.com/polymer_Hexcel-HexTow-AS4-Carbon-Fiber.php (accessed on 17 October 2023).
18. Dragonplate. HexTow® AS4 carbon fiber. Available online: https://dragonplate.com/images/uploaded/pdfs/fiberspecs/as4_hextow_datasheet.pdf (accessed on 17 October 2023).
19. Jelena M, Brcković L, Gajović A. Influence of preparation method and alumina content on crystallization and morphology of porous yttria stabilized zirconia. Journal of the European Ceramic Society 2017; 37(9): 3137–3149. doi: 10.1016/j.jeurceramsoc.2017.03.026
20. Sharif AA, Mecartney ML. Superplasticity in cubic yttria stabilized zirconia with 10 wt.% alumina. Journal of the European Ceramic Society 2004; 24(7): 2041–2047. doi: 10.1016/S0955-2219(03)00354-6
21. Ai Y, Xie X, He W, et al. Microstructure and properties of Al2O3(n)/ZrO2 dental ceramics prepared by two-step microwave sintering. Materials & Design (1980–2015) 2015; 65: 1021–1027. doi: 10.1016/j.matdes.2014.10.054
22. Özgür TC. Investigation of the Effect of Different Materials and Constructions on Impact Resistance of Vehicle Bumpers (Turkish) [Master’s thesis]. T. C. Bursa Uludağ Üniversitesi Fen Bilimleri Enstitüsü; 2020.
23. Dashairya L, Chaturvedi V, Kumar A, et al. A benign strategy toward mesoporous carbon coated Sb nanoparticles: A high-performance Li-ion/Na-ion batteries anode. Solid State Ionics 2023; 396(1). doi: 10.1016/j.ssi.2023.116243
24. Najmi L, Hu Z. Effects of carbon nanotubes on thermal behavior of epoxy resin composites. Journal of Composites Science 2023; 7(8): 313. doi: 10.3390/jcs7080313
25. Najmi L, Zebarjad SM, Janghorban K. Effects of carbon nanotubes on the compressive and flexural strength and microscopic structure of epoxy honeycomb sandwich panels. Polymer Science, Series B 2023; 65(2): 220–229. doi: 10.1134/S1560090423700872
26. Sayman O, Duranay M, Gür M, Koçak S. Elastic-plastic stress analysis of a thermoplastic composite disc under uniform temperature distribution. Science and Engineering of Composite Materials 2006; 19 (1): 61–77. doi: 10.1515/SECM.2006.13.2.139
27. Dai T, Dai HL. Investigation of mechanical behavior for a rotating FGM circular disc with a variable angular speed. Journal of Mechanical Science and Technology 2015; 29(9): 3779–3787. doi: 10.1007/s12206-015-0824-4
28. Çallıoğlu H. Stress analysis of functionally graded isotropic rotating discs. Advanced Composites Letters 2008; 17(5). doi: 10.1177/096369350801700501
29. Timoshenko S, Goodier JN. Theory of Elasticity. McGraw-Hill; 1970.
30. Drelich J, Tormoen GW. Beach ER. Determination of solid surface tension at the nano-scale using atomic force microscopy. In: Mittal KL (editor). Contact Angle, Wettability, and Adhesion. VSP; 2006. Volume 4. pp. 1–28.
31. McCartney LN. Predicting properties of undamaged and damaged carbon fibre reinforced composites. In: Beaumont P, Soutis C, Hodzic A (editors). The Structural Integrity of Carbon Fiber Composites. Springer; 2017. doi: 10.1007/978-3-319-46120-5_16
32. Chegg. Available online: https://www.chegg.com/homework-help/questions-and-answers/1-20-fiber-composite-consisted-as4-carbon-fibers-3501-6-epoxy-matrix-engineering-constants-q45618630 (access on 15 September 2023).
33. Apatay T, Eraslan AN. Elastic deformation of rotating discs of parabolic thickness, analytical solutions. Gazi University Journal of Faculty of Engineering and Architecture 2003; 18(2): 115–135.
34. Çallıoğlu H, Sayer M, Demir E. Stress analysis of functionally graded discs under mechanical and thermal loads. Indian Journal of Engineering & Materials Sciences 2011; 18: 111–118.
35. Sayman O, Yanginci S, Sayer M. Thermoelastic-plastic stress analysis in a thermoplastic composite disc. Journal of Reinforced Plastics and Composites 2005; 24(1): 21–33. doi: 10.1177/0731684405041716
36. Leopold WR. Centrifugal and thermal stresses in rotating discs. Journal of Applied Mechanics 1984; 15(4): 322–326. doi: 10.1115/1.4009854
37. Manjunath TV, Suresh PM. Structural and thermal analysis of rotor disc of disc brake. International Journal of Innovative Research in Science, Engineering and Technology 2013; 2(12): 7741–7749.
38. Joshi P, Samantray S, Prabu SS. Investigation on thermal stress analysis of brake disc using ANSYS simulation. ECS Transactions 2022; 107(1): 10865. doi 10.1149/10701.10865ecst
DOI: https://doi.org/10.59400/n-c.v2i1.234
(120 Abstract Views, 89 PDF Downloads)
Refbacks
- There are currently no refbacks.
Copyright (c) 2023 Hüseyin Fırat Kayiran

This work is licensed under a Creative Commons Attribution-NonCommercial 4.0 International License.
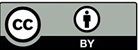
This site is licensed under a Creative Commons Attribution 4.0 International License.
.