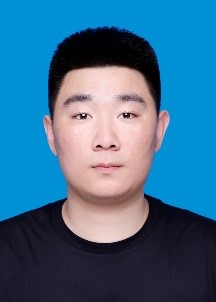
Section Collection Information
Dear Colleagues,
Novel composite materials and structures draw increasing attention due to their high mechanical properties and lightweight performance, showing great potential applications in automotive, aerospace and other industries. However, traditional processing methods, such as casting, machining, injection molding and hot press molding limit the manufacture of complicated structures. 3D printing, also known as additive manufacturing, provides solutions for manufacturing composite structures with high functional performance. The section of the Materials Technology Reports, “Advanced Composites”, aims to present the latest advances focusing on novel composite materials and structures processed by advanced additive manufacturing (e.g. fused deposition modeling (FDM), selective laser sintering (SLS), selective laser melting (SLM), and stereolithography (SLA), etc.). In this section, we invite you to submit a manuscript studying but not limited to novel materials, structural design and optimization, advanced processing methods, etc. It is welcome that the investigations on the compressive and impact behaviors of 3D printed composite materials (metals or polymers) and structures, but not limited to the mechanical properties. In this section, original research articles and reviews are welcome. Research areas may include (but not limited to) the following:
l Materials characterization for additive manufacturing (e.g. advanced matrix material, short fiber-reinforced composite, continuous fiber-reinforced composite, etc.);
l Advanced post-processing technology for 3D printed materials (e.g. heat treatment, hot isostatic pressing, etc.);
l Constitutive modeling of 3D printed materials under extreme mechanics and environments (e.g. high strain rate effect, extreme ambient temperature, etc.);
l 3D printed functional materials and structures (e.g. shape memory polymer and composite, metamaterials, and multi-functional material, etc.);
l Compressive and impact behaviors of 3D printed composite structures (e.g. thin-walled structures, honeycomb structures and lattice structures, etc.);
l Collapse mechanisms and theoretical modeling methods;
l Bio-inspired and fractal structural design methods and composite structures.
We look forward to receiving your contributions.
Dr. Jin Wang